Innovative Process Improvements Require a Short and Long Term Connection
Innovative process improvements can be defined as discovering avenues that are ground breaking and far-reaching. Improving business processes on a large scale requires overcoming roadblocks. Three of the most common barriers are:
- Hard to implement solution
- Further analysis of solution needed
- Solution solves symptom but not the root cause
Companies often make process changes with small tweaks to achieve immediate results. Long-term innovation is lost because the hurdles are high and implementation time is longer. To avoid this trap, leadership in companies (at all levels) need to be continuously engaged. Active engagement
involves placing great importance to process improvements and innovative ideas at every available opportunity. To spawn innovative process improvements, insist on a mix of short and long term process changes.
Customer Directed Value Stream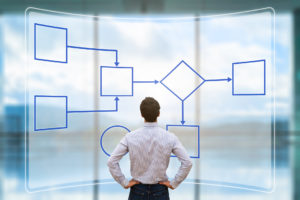
For your business to achieve the best results, feedback from your customers is needed. The information will provide valuable insight into your process from the eye’s of your customer. Customer Input will spawn new, innovative process improvements. Creating and keeping alive a business Value Stream Map will incorporate valuable customer feedback. Determination of success is ultimately based upon customer perception. Business savings of time and cost from improved efficiency are great, but a tie-in to the customer provides continual innovation and greater success. Consequently, creation of a Value Stream Map is important – customer insight is preserved.
Leaders Must Learn to Fail Successfully to Achieve Innovative Process Improvements
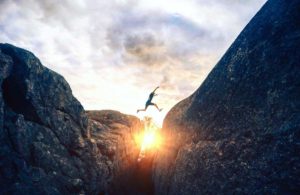
Moving innovative process improvements forward requires learning from failures as a critical step. As a result, leaders must be able to share and encourage all employees in their successes or failures. A culture of Learning to fail successfully is the key. When the occasional failure occurs, leaders must encourage action and support their teams versus look for blame. Encouragement will help teams learn from their mistakes. As a result, innovative process improvements are more achievable. By empowering your teams with your constant support, innovative process improvements are more within reach. Provide access to experts and guide teams by establishing a process improvement culture. Award teams that succeed and lift teams that fail.
Adopt the Tools that Work for Your Business Culture
Many process improvement methodologies exist including Lean, Six Sigma, Theory of Constraints, TQM, etc. Practical adoption of these methods to fit the current business culture is key. Innovative process improvements are more plausible when your teams aren’t first trying to become experts in a methodology.
Despite what method is used, accommodations must be made for testing outcomes throughout the improvement process (i.e., making a small batch run in manufacturing facility). Continuous learning is key with test, try, and adopt philosophies. Companies should educate their employees in basic principles of improvement and problem-solving methods, and then turn them loose to create a customer driven Value Stream Map.
Business Ready Innovative Process Improvements
Establish a comprehensive budgeting cycle that provides a good mix of short term and long term projects. One of the best methods I’ve seen to accomplish this is by establishing a business Value Stream Map. Once the current state is defined, a vision of the future is set enabling everyone to plan around the same objective. As a result, short and long term projects work in concert.
Link your Business Strategy and Process Improvement Initiatives – Find Out More HERE